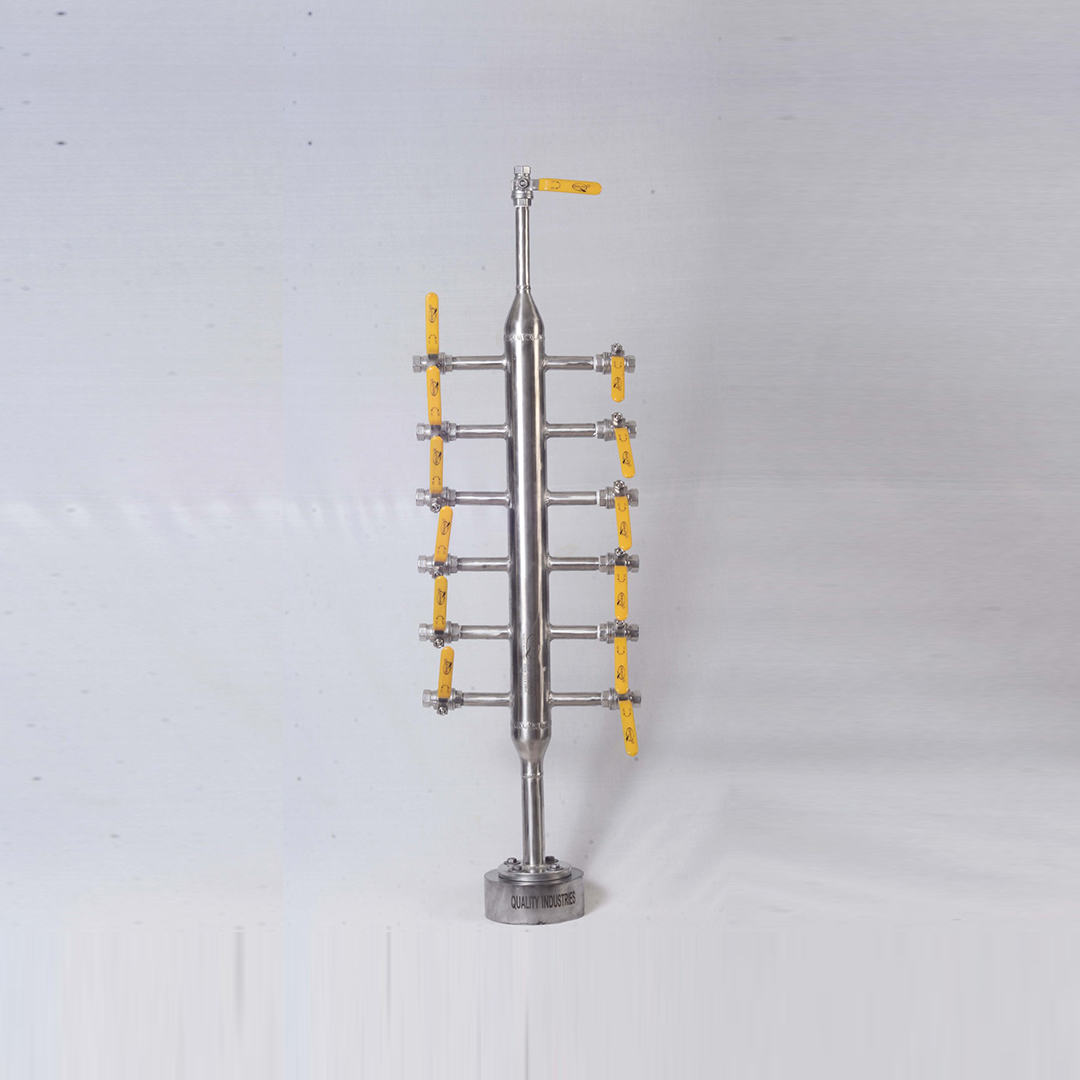
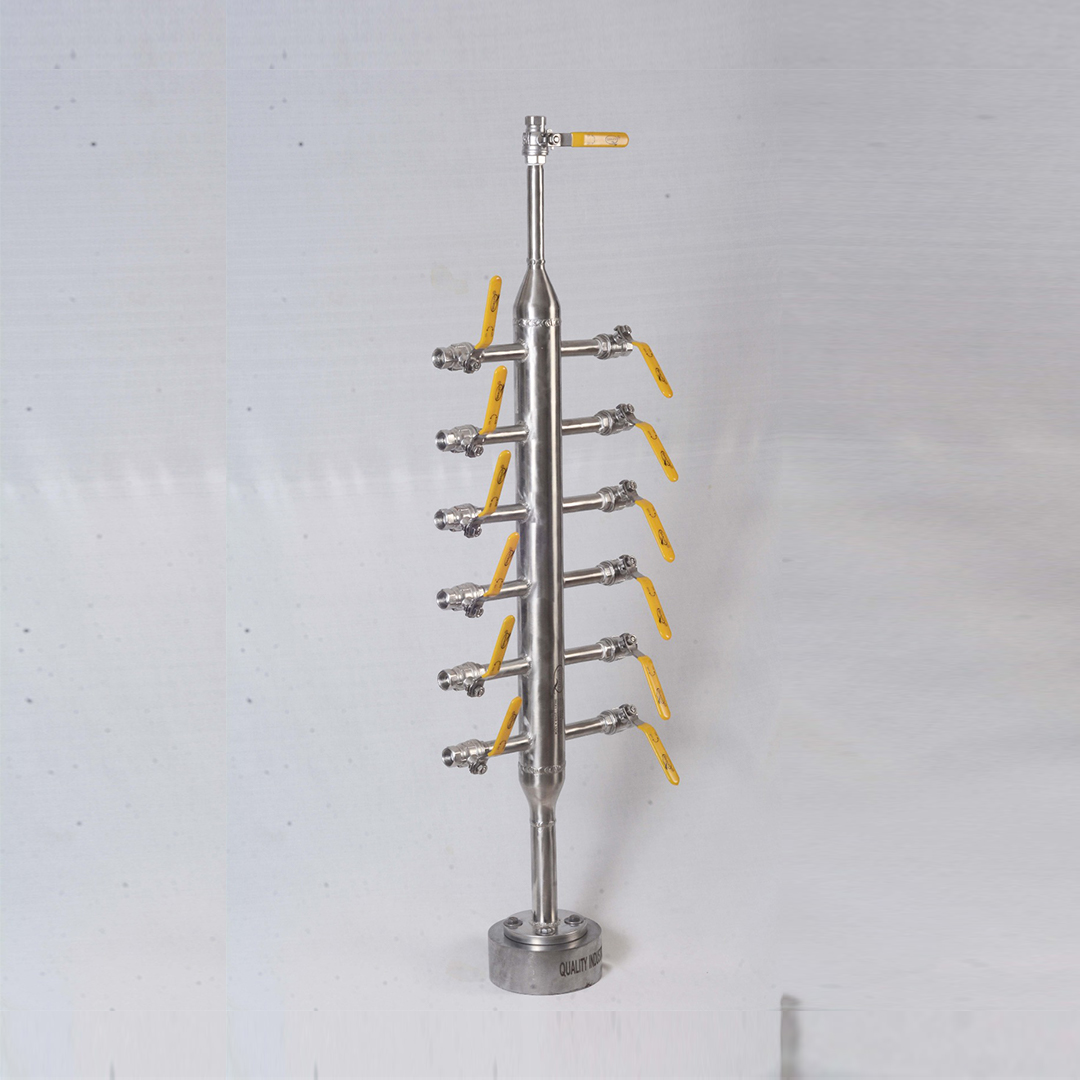
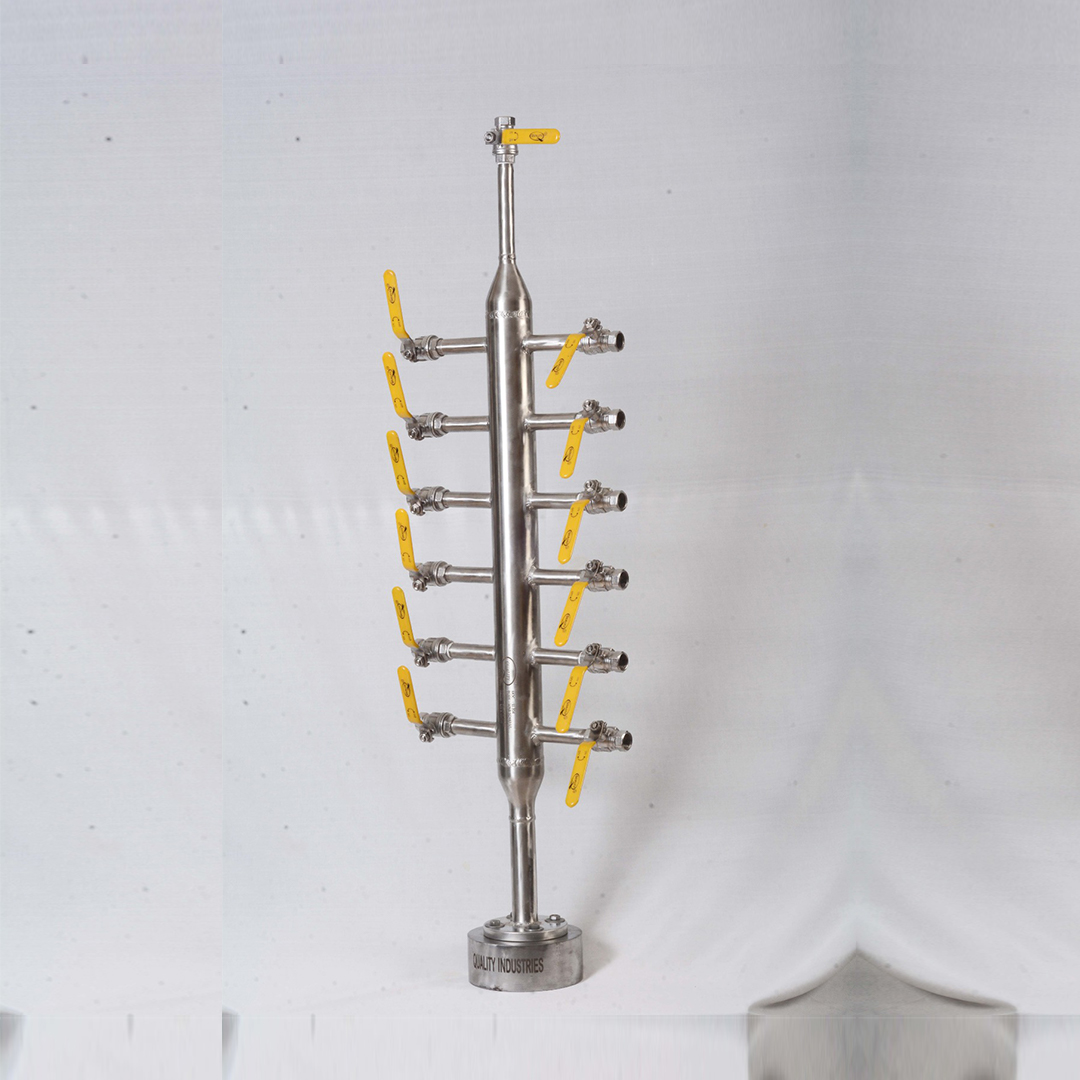
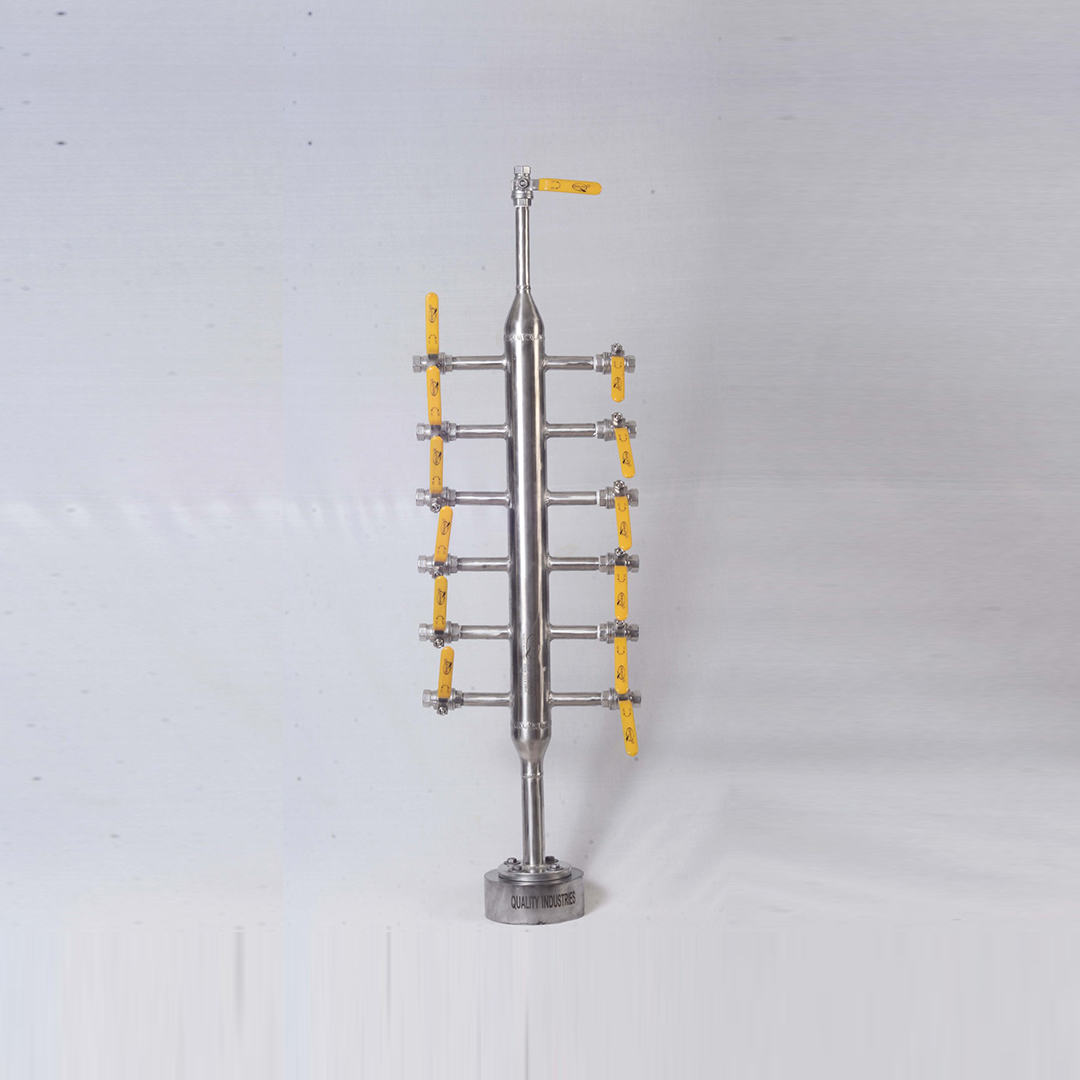
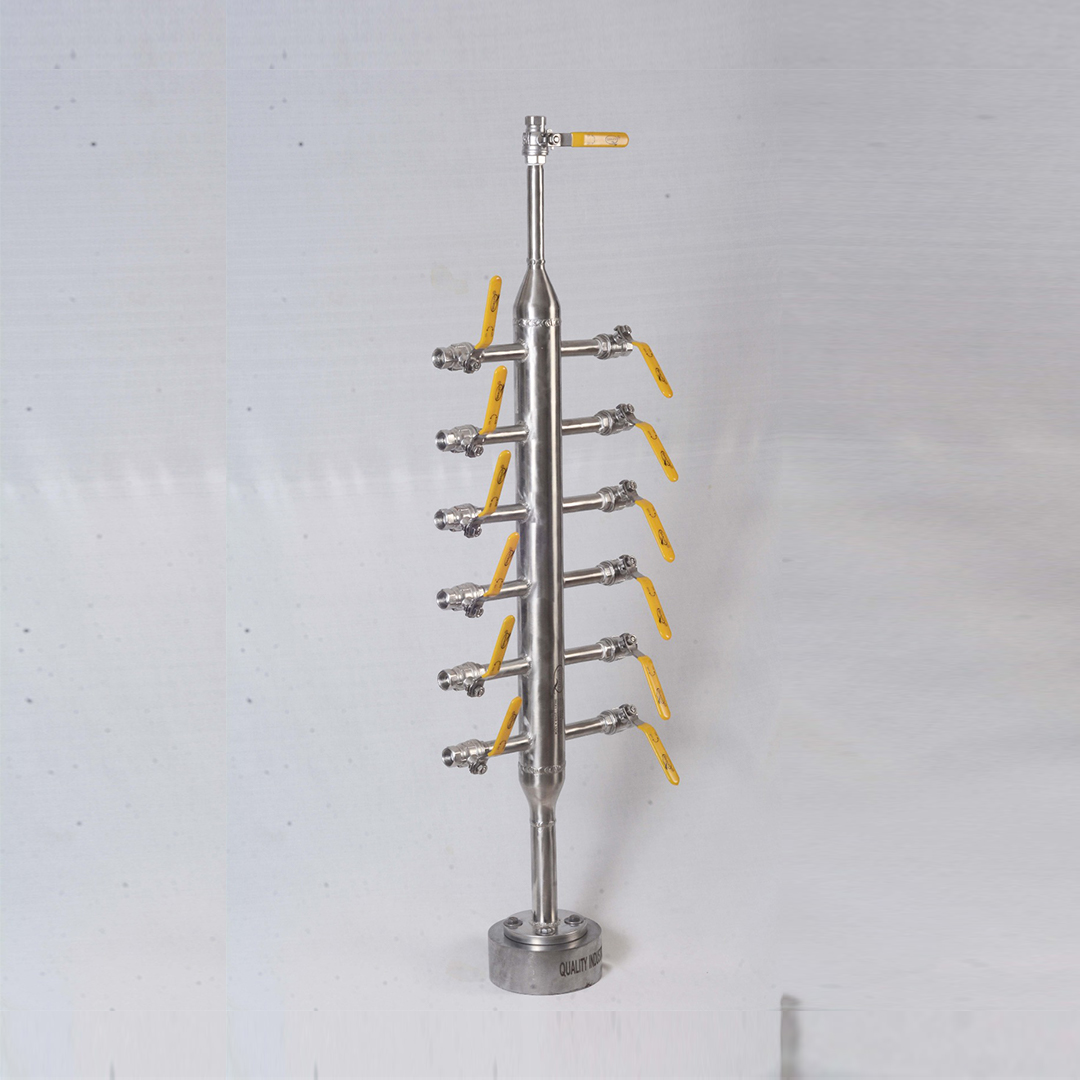
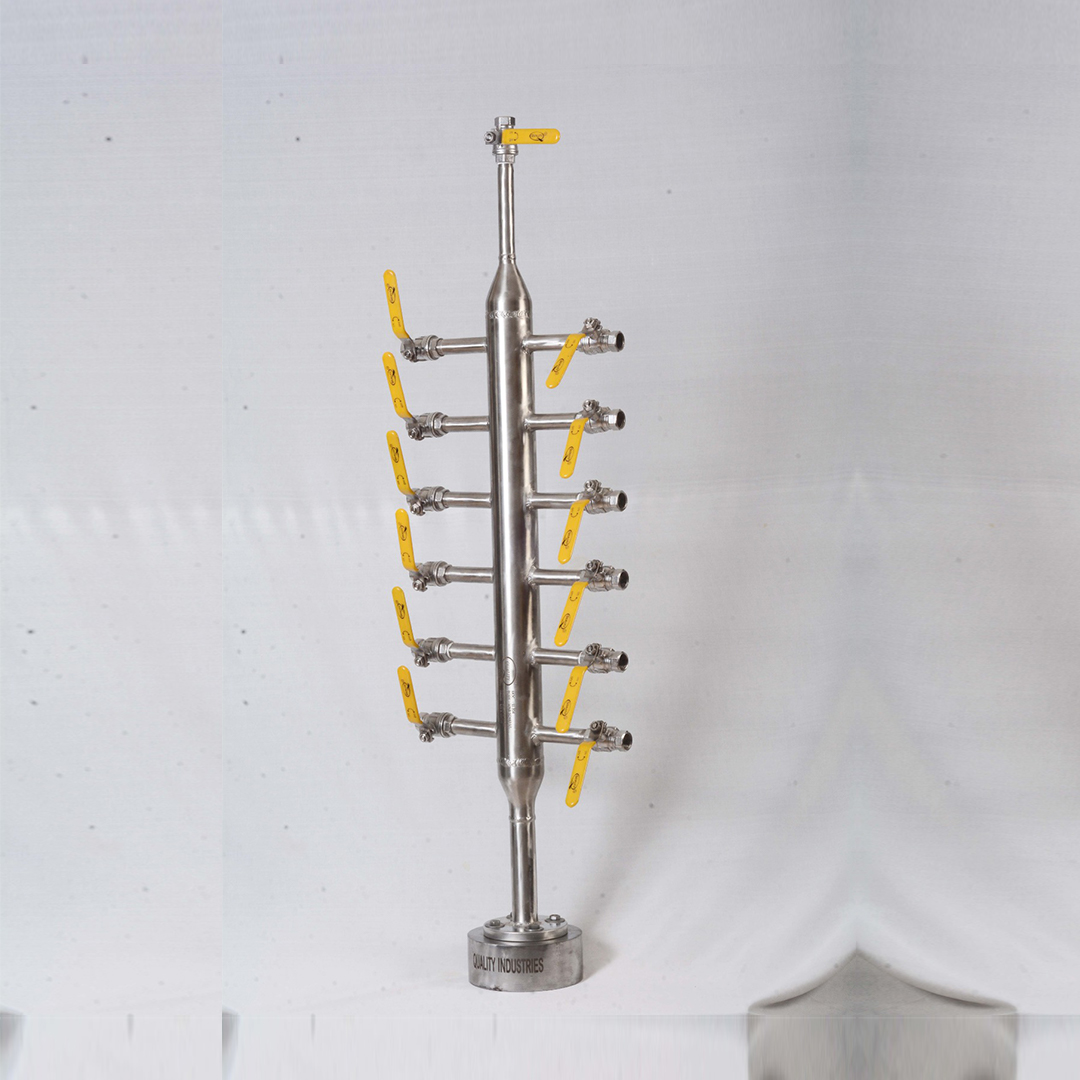
Air Headers Manufacturer
Quality Industries is a Leading Air Headers Manufacturer, Supplier and Exporter From India. The air header is a pipe connected with a number of valves, each having one inlet and one drain at the end of the pipe, and in between are numerous outlets and valves connected to the body. Outlet ports can be from 4-way up to customer requirement; inlet and drain connections can be flanged; coupling, ball valve, needle valve, etc. as per requirements. Air headers are mainly used for air distribution and to centralize multiple connections.
Schedule 40, 80, and 160 are available (larger sizes can also be provided upon request), with standard material as SS316 or as specified. All of our air headers are factory-tested.
Frequently Asked Questions
An air header is a device used to distribute compressed air from a single source to multiple outlets or instruments in an industrial setup. It serves as a centralized distribution point, ensuring efficient air supply to various equipment or tools.
An air header works by receiving compressed air through a main inlet and distributing it evenly through multiple outlet ports. Each outlet port can be connected to different pneumatic instruments or tools, allowing for simultaneous operation.
Air headers are commonly used in industries that rely on compressed air systems, such as:
- Oil and gas
- Chemical and petrochemical plants
- Power generation
- Manufacturing facilities
- Water treatment plants
Air headers are typically made from:
- Stainless steel
- Carbon steel
- Aluminum
- Brass
Needle valves are made from various materials, including:
- Efficiency: Centralizes air distribution, reducing the need for multiple air lines.
- Space-saving: Compact design minimizes space requirements in industrial setups.
- Versatility: Can be customized with various outlet configurations to suit different needs.
- Durability: Made from robust materials to withstand high-pressure environments.
Yes, air headers are designed to handle high-pressure applications and are often used in systems with demanding pressure requirements. The design and material choice should match the system's maximum operating pressure.